Every day, the news shows that despite the implementation of safety management systems, some of which are certified and recognized as effective, companies are still faced with accidents, the consequences of which can be fatal.
Safety Golden Rules, a life-saving phrase
Based on this observation, it was necessary to bring a new dynamic to the risk prevention approach, by moving away from the systemic and relatively complex aspect, towards a new communication tool that was understandable, simple and effective.
In fact, the society and working environment in which we evolve every day are based on a multitude of rules: rules of conduct, regulations, etc. It therefore seems appropriate that specific rules should be written in a guidebook to ensure the health and safety of employees in the performance of their duties.
Over the past few years, companies have decided to set up a process for identifying and communicating Safety Golden Ruleswith the main aim of reducing incidents and accidents in the workplace.
A new tool for occupational risk prevention
These rules are being deployed mainly by construction and industrial companies operating in France and abroad.
In so far as the approach is supported by companies located all over the world, the notion of Safety Golden Rules can be called by different names:
- Règles fondamentales,
- Règles qui sauvent,
- Life saving rules,
- Golden Rules, …
They are identified by a company aiming to prevent its major risks as far upstream as possible. It is essential to follow a detailed methodology that enables systemic and operational data to be cross-referenced, to have a global vision and achieve a result that is as close to reality as possible.
The challenges and limits of a new prevention approach
Deploying a risk anticipation approach within a company is often a challenge. Internal resources do not always have the skills, expertise and tools required to carry out the Project successfully.
In addition, there is no recognized public methodology for identifying golden rules, which represents a challenge for HSE personnel wishing to initiate the process.
Besides resource constraints, the success of such an approach depends on effective change management during the communication and appropriation steps.
The"Safety Golden Rules" Steering Committee.approach is based on 5 key objectives:
- Demonstrate Management commitment and involvement,
- Identify high-risk work situations,
- Implement relevant and effective measures,
- Improve working conditions, provide protective equipment and the necessary resources,
- Train staff in new safety rules and ensure they are respected.
A tool to strengthen the workplace safety culture
On the strength of its experience and success in helping its customers developing their Safety Golden Rules Aegide International would like to share with you the key steps of the "Safety Golden Rules" Project for a successful deployment.
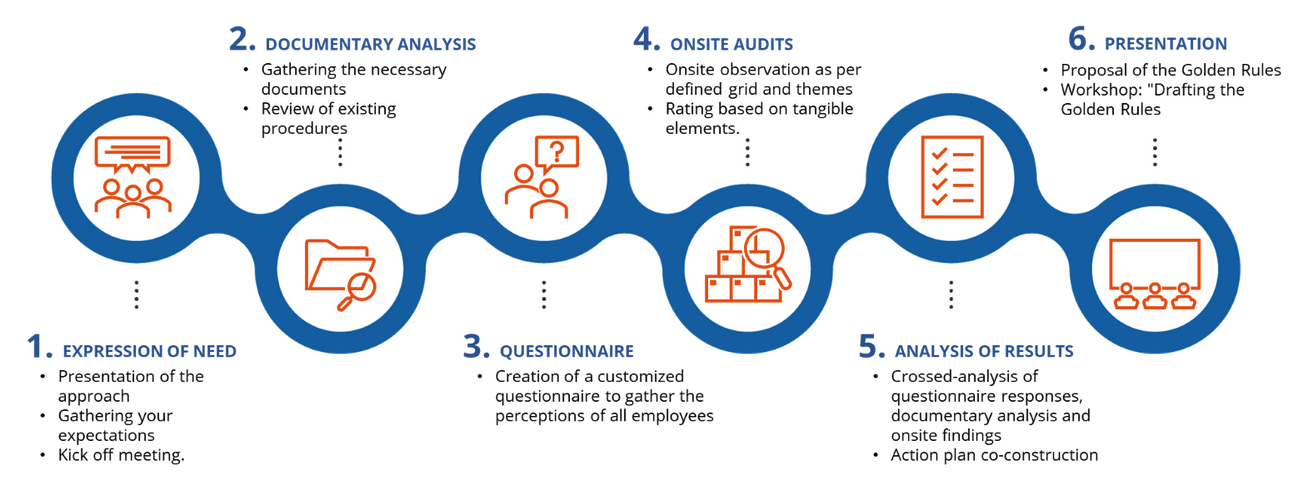
The different steps for the successful implementation
We have identified a series of steps to implement a Safety Golden Rules approach properly.
1st Step: Expression of need
The first step is to clearly define the Company's needs and expectations with Management, and to present the methodology developed by Aegide International. It enables to verify the consistency between the Company's needs, the methodology and the proposed deliverables. Once this activity has been completed, the findings are summarized, presented, and approved during the Kick-off Meeting by the"Safety Golden Rules" Steering Committee. »
To initiate the Project in proper manner, it is essential to set up a"Safety Golden Rules" Steering Committee.made up of representatives from all levels of management, each department, and representative organization.
The aim is to provide all members the same level of information, to be able to express themselves, particularly on behalf of their colleagues, and forward the information. Subsequently, cross-functionality is a source of different visions, ideas, and interesting arguments to promote Safety Golden Rules and ensure all employees adhere to the content.
The Committee meets periodically to report on Project progress.
Aegide International acts as a facilitator for the Steering Committees, ensuring that the objectives of each step are clearly presented, understood, and achieved.
2rd Step: Documentation review
For this second step, it is essential to understand how the company is organized and how it operates, by sharing safety management system documentation to enable analyzing it.
To measure the management system performance and assess health and safety results, it is mandatory to review the following documents.
- Health & Safety Policy: Reflects the Company's commitment and the resources deployed to implement risk management approach.
- Objectives and Indicators: Provide a quantitative and visual representation over several years of the Company's performance in terms of Occupational Health and Safety (OHS).
- Procedures and Guidelines: Present the Company's operational activities. They provide a precise understanding of the tasks performed by employees, the associated risks and the resources provided.
- Competency management and job descriptions: Useful for assessing the human resources and skills management.
- Risk Assessment: Allows evaluating the level of relevancy between the activities described the ratings and the mitigation actions implemented.
- Accident Reports: Enable assessing the consistency between workplace accidents, conclusions and corrective actions taken.
- Action Plan: Measures the Company's commitment and proactivity in its improvement process.
An exhaustive list of the documentation to be provided is drawn up in Step 1, to ensure that all activities are covered by the documentation review.
3rd Step: Questionnaire
The aim of the questionnaire is to understand how employees perceive the safety management system through 12 themes.,It enables identifying the system's strengths and weaknesses, as per employees’ point of view.
The results of the questionnaire are analyzed and compared with onsite’audit ones.
4rd Step: Onsite audit
The onsite audit is prepared and conducted according to a standardized methodology as shown in the diagram below:

The onsite audit is carried out as per a grid specifically developed for the Company, considering the results of the questionnaire, to propose accurate Safety Golden Rules.
Audit assessment is based on a 5-level rating scale, as shown below:
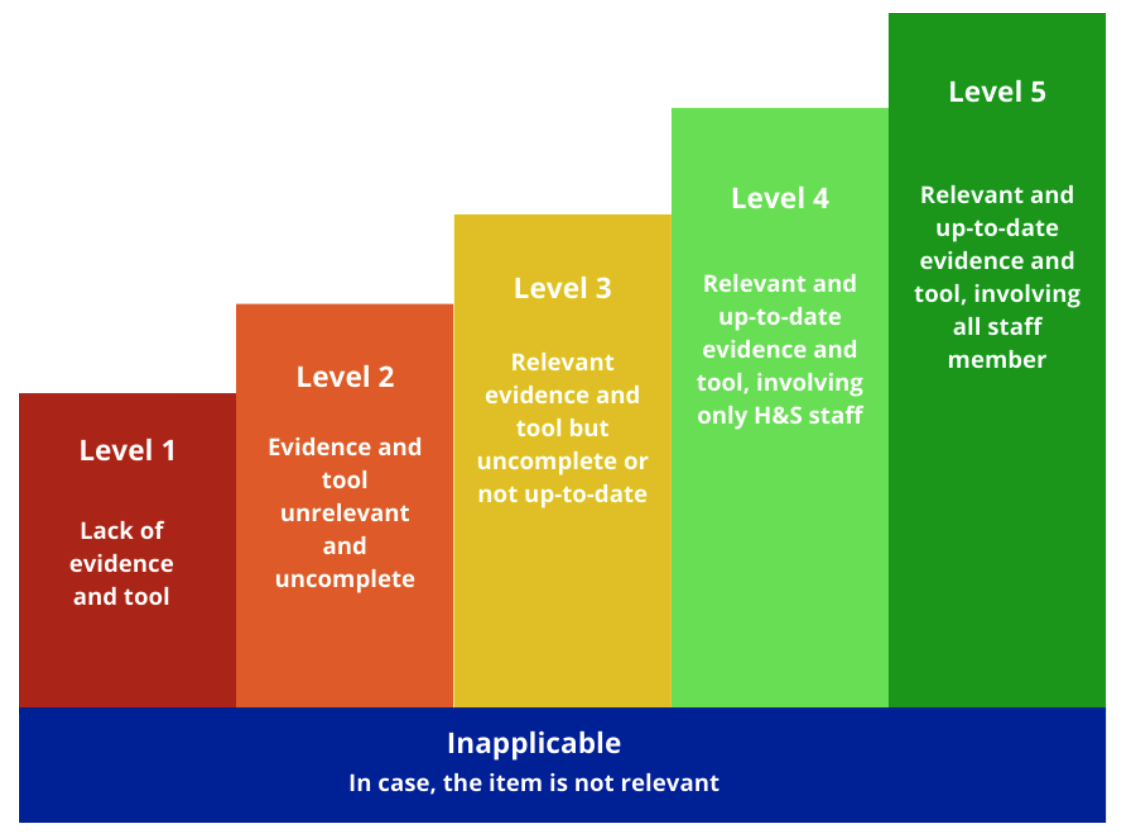
The auditor defines the most appropriate score for each item, based on recorded evidence. A comment is added to justify the score for each item.
During the Close-out Meeting, the auditor presents the preliminary findings: the hazards and themes which are mastered, and those with weaknesses.
5rd Step: Analysis of results
Result analysis is a crucial stage in the project to identify Safety Golden RulesIt involves cross-referencing the following data:
- Health and Safety accidentology indicators (Quantitative from company)
- Questionnaire responses (Qualitative from employee)
- Onsite audit results (Qualitative from auditor)
Based on these data, it is possible to identify and prioritize hazards and themes.
The elements identified as priorities are spotlighted and form the basis for drawing up Safety Golden Rules.
In addition to the analysis, a draft Action Plan is proposed to improve the performance of each item.
In the case of a multisite organization, steps 3 to 5 should be carried out iteratively,, to collect and analyze site-specific data, and then conclude.
6rd Step: Presentation of results
This final step consists in presenting the results of the analysis to the"Safety Golden Rules" Steering Committee. ».
During presentation meeting, the Aegide International team shares its conclusions based on the analysis previously carried out. It presents the priority themes requiring particular attention, to convert the main risks identified into prevention opportunities.
The Golden rules are drafted in a collaborative manner and are presented to the steering committee for validation. This step marks the end of the project.
The following steps consists in:
- Developing Safety Golden Rules Guidelines,
- Creating sensitization and communication materials,
- Communicating and raising employee awareness.
A customizable tool
The Safety Golden Rules tool adapts to your needs, and to the hazards of your organization. A standard list of 12 hazards is available and can be customized to suit with your activities.
When it comes to customizing indicators, additional quantitative data can be considered, if they provide added value in identifying the Safety Golden Rules of the company
Finally, as previously stated, the tool offers the option of creating a customized Action Plan based on the maturity level of each item. This action plan is deployed to reinforce the safety management system and operational control, to ensure continuous improvement.